Rigid-flex PCBs come with several advantages as compared to conventional rigid boards. This hybrid circuit board design integrates elements from both hardboard and flexible circuits, giving you better quality control and prototype performance.
Today, it is present in all electronics and is manufactured widely. Some of the key benefits of a rigid-flex PCB is its slim profile and versatility that supports simple and complex applications for military purposes, medical devices, aerospace, etc.
Rigid PCB cannot be like flexible PCB as the former one cannot be twisted or moulded into any shape. Moreover, it is made up of copper trances which can be incorporated on a single board to connect the different components on board.
The material of the base is made up of rigid substrate which gives strength and rigidity to the board.
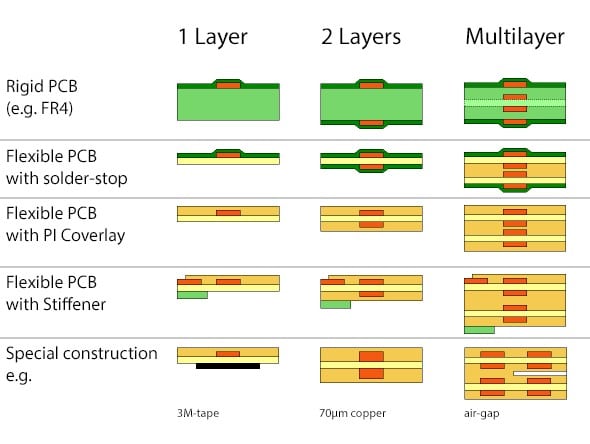
Make sure you rely on a professional and experienced PCB prototype manufacturer for reliable and high-quality PCBs.
Today, designing a rigid-flex PCB is considered more challenging than the traditional rigid PCB. In this blog, we will give you good reasons why you should use a rigid-flex PCB.
Rigid and Flexible PCB hold their own drawbacks and benefits in terms of ease of use and availability. Both of these are used to connect multiple electronic components on circuit boards. Read to know more…
Advantages of Rigid-flex PCB and Its Manufacturing Process
Improves the reliability of the circuit
The primary purpose of connectors is to remove the wire harness from the PCB. Adding connectors to the PCB can be more dangerous if you’ve multiple interlinking subcircuits. Incorporating a rigid-flex design will reduce the need for board-to-board connectors. It will also enable lesser solder joints, which means fewer connection issues.
Thus, connection reliability increases due to fewer points of potential failures. In addition to this, it can also improve your electronic applications’ performance due to the reduced impact of vibration, contributing to less premature circuit failures.
Adds flexibility in design
The rigid-flex PCB has multiple layers of flexible circuits, which offers increased flexibility to fit into even the smallest device. You don’t need to design a device that resembles the PCB specifications like a rigid board. All the corners of the rigid-flex PCB are designed to provide a flexible connection. It also gives you the freedom to add rigidness whenever you require mechanical support.
Emits less noise
The main function of a rigid-flex PCB is to emit less noise in an application. All the components of the rigid-flex PCB should be manufactured to bring radiation emission at the least. It works by reducing the radiation and electric current, which in turn reduces electromagnetic waves and significantly minimizes the noise produced by the components
Occupies less space
Here, space is a luxury. Handheld thermal scanners should adhere to rigid-flex PCB designs since they don’t require much space to fit in the wire harness. Interconnecting circuit, when built-in on a flexible substrate, gives more room to route the traces.
Lessens manufacturing cost
Owing to its small size and few connections, less material is required to assemble rigid-flex PCB. Not only this, fewer parts and connector assemblies increases the yield and purchasing cost of the final product. Less number of connections can pose a serious risk within the supply chain of your electronic devices.
In a nutshell: Logistical and assembly costs are reduced significantly.
Tolerates high temperatures and aggressive conditions
The polyimide of high thermal stability is used in designing rigid-flex PCB – this makes it temperature resistant. This is the reason why it’s a credible choice for complex military and defence applications. Rigid-flex PCB has the best of both rigid and flex boards; this makes it resistant to harsh ultraviolet rays, harmful radiations, toxic oils, extreme shocks, and other industrial conditions.
Allows automating testing
You can easily automate testing as all the subcircuits are interconnected. This gives the ability to eliminate connectivity issues even before the components are assembled, preventing unnecessary wastage. Gladly, it’s also budget-friendly if you choose a genuine PCB maker.
Enables easy maintenance
The simple design of a rigid-flex PCB gives you the convenience of repairing and maintaining it accordingly. Unlike other rigid circuits, this one marks all the components, making it easy to assemble and disassemble whenever required. Moreover, its signal paths are exposed and arranged systematically, which makes it easy to detect any issues and repair them simultaneously.
Author Bio
Laura Stevens works as a digital marketing manager at PCBGOGO. PCBGOGO manufactures high-quality PCBs and provides the best PCB assembly services that are affordable and effective. In her free time, she writes informational blogs and articles that aim at helping people.
Website: https://www.pcbgogo.com/