Machine vision and robotics employ a variety feedback mechanisms to ensure precision. The process of identifying 3-D space with accurate accuracy can be accomplished by a variety of methods. At present optical, sonic and sensing and mechanical methods have been used with sufficient achievement. The more demanding demands force us to make our pencils sharper. The next generation of vision-based designs are based on greater precision in volume and depth sensing and greater precision.
Common common sense
The methods used up to now have worked for the specific problems. The cheapest sensors for surface or depth can be as basic as a linear trimpot that is spring-loaded and limit switch.
In terms of precision optical and sonic techniques are more reliable without the requirement for moving components. Optic distance sensing is utilized to detect proximity and for more precise range detection. The distance of less than millimeter up to 8 meters can be identified as a digital signal that indicates whether or not there is an object.
With the cost-effective high-resolution, low-cost modern generation of cameras, video technology has been at the forefront of volumetric and distance measurement. The latest design trends and demands force manufacturers of devices to create top-quality solutions.
More Options to Choose from
In addition to the need for machines with greater precision and higher precision, post-pandemic conditions brought about the need to identify the presence of people and occupancy figures in any given area. Spacing between individuals is a fairly new feature that people are required to include. Another condition that requires care is dementia. In assisted living facilities, the capacity to have a comprehensive computer system to track patients’ movements is essential.
Factory and industrial applications also benefit from more reliable and precise measurements of volume and distance systems. As advanced fabrication technology develop and become integrated feedback on the accuracy of position, direction as well as speed and depth is crucial for future-generation fabrication equipment. For instance milling machines are dependent heavily on the precision of motors as well as gear assemblies that precisely position grinding and cutting heads. Too deepand the cutting head can break. Too shallow and too much material remains. The machines will find the correct spot using precise distance sensing, even when calibration is not correct. Closed loop feedback yields more efficient outcomes. Machines that use CNC, 3D printers as well as laser/plasma cutting and welding machines benefit from greater accuracy of feedback in closed loops.
Innovative New Products
Analog Devices anticipated a growing demand for volumetric sensing and measurement in a variety of applications. The AD-FXTOF1 is a modular video engine, with an embedded Time of Flight (ToF) distance measurement included (Figure 1.).
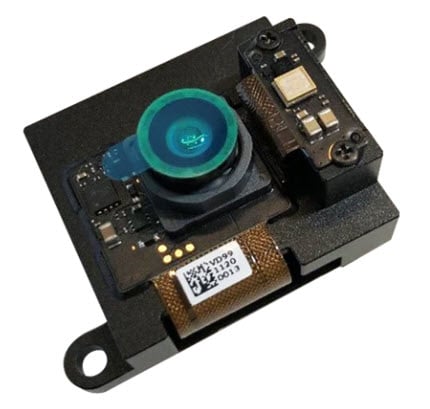
Figure 1: The modular 3-D sensing development kit supports various applications from volumetric measurement to occupancy and activity detection. (Source: Analog Devices)
This VGA resolution, 640×480 pixels at 30 frames/second facilitates the easy integration of an interface to a host’s application supervisor. It has two lanes of mobile industry Processor Interface (MIPI) which can be connected via a 25-pin cable or a 15-pin flex cable with connect to an interposer.
940nm IR laser is an eye-safe, vertical-cavity surface-emitting laser (VCSEL) that helps reduce manufacturing expenses by eliminating the right-angle emitter configuration. It is also praised for its ability to function in bright conditions due to the optical bandpass filter of 940nm. This filters out interference and noise from outside sources. A batwing-style diffuser can be utilized to provide the receiving lens with a precise 87-degree x the 67-degree field of view.
In terms of performance, the video depth finder features two different settable ranges that it operates within. The 20cm-180cm range and a 50cm-300cm range that maintains the accuracy of 2 percent. It requires an AC power supply with 5V2A that is rated between -20oC and +75oC. It is therefore robust and durable ecologically.
The SDK development kit interface lets it connect to host microprocessors or microcontroller as well as single-board computers such as Raspberry Pi or Nvidia ( Figure 2.). The SDK also comes with OpenCV as well as Open C/C++ Python (r), MATLAB (r), Open3D, and RoS wrappers that allow developers can utilize them to speed up the development of their applications. Connectivity choices are USB, Ethernet, or Wi-Fi. Additionally, reference designs as well as bill of material are included.

Figure 2: The actual camera and lens RFPC board and image processing AFE boards use IIC interfaces for control and configuration. Operational GPIO and MIPI interfaces allow real-time control and data access. (Source: Analog Devices)
Conclusion
The requirement for quick and precise distance and image sensing allows designers to design the next generation of sensors, robots vehicles as well as security systems. The AD-FXTOF1 of Analog Devices lets you test the water in a short time and with ease. Expect greater resolution, higher frame rates and greater distances in future version of this tech when it becomes widely used in industrial and domestic applications.